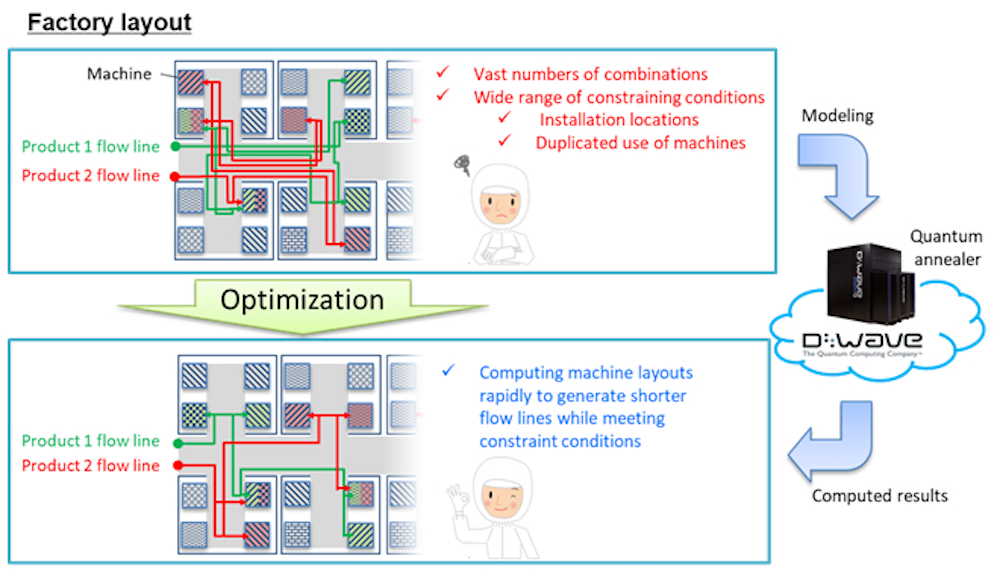
Diagram illustrating flow line optimization - Source OKI
Quantum computers hold significant promise for dramatically increased computational power compared to conventional computers. Related development work is currently underway worldwide. In Japan, quantum technologies, including quantum computer technologies, are regarded as an important fundamental technologies, on which advances are being made in research and development on a national scale. While development continues, D-Wave in Canada achieved a world's-first in 2014 by launching a commercial remote access service based on quantum computers known as quantum annealers(*2), specifically tailored to solve combinatorial optimization problems. This development spurred hopes for practical applications. OKI is involved in research and development on related practical technologies, based on the conviction that the usefulness of quantum computer technologies will be widely recognized and play an integral role in society in the not-too-distant future. At OKI Data's LED Management Factory, OKI tackled the task of machine layout optimization to validate the basic computing technologies required to solve real-world issues, which OKI had established in these efforts, by applying these technologies in in-house case studies.
As the working population in Japan shrinks, labor shortages are becoming an increasingly serious issue in manufacturing industries. Improving productivity at manufacturing sites has become a major and pressing social issue directly affecting manufacturing costs. At the LED Management Factory operated by OKI Data, multiple products are manufactured with different manufacturing processes using tens—or even hundreds—of different semiconductor manufacturing machines, with workers constantly moving between machines. Improving productivity here requires optimizing machine layouts to minimize distances traveled by workers ("flow lines"). However, as the numbers of machines and different types increase, the number of possible combinations increases exponentially. In the case examined here, this easily exceeds a googol (10 raised to the power of 100). Due to the need to account as well for complex constraints, including machine installation locations and methods of selecting duplicate machines, it was unfeasible to determine optimal machine layouts by calculating all of these parameters—even using a super computer or other high-performance conventional computer.
OKI and OKI Data used a quantum annealer provided by D-Wave to tackle this layout optimization. From a research perspective, a quantum annealer offers the advantage of facilitating quantitative observations of the results of the optimum layouts computed. However, to solve the problem in an efficient way, a new algorithm suited to constraints involving both the quantum annealer and the manufacturing site was required, making the involvement of personnel familiar with the manufacturing site absolutely essential. For this reason, personnel from the LED Management Factory were involved in the process to successfully design a computational algorithm in-house by modeling the conditions that apply when manufacturing two types of products involving different manufacturing processes and production quantities within the same factory. A quantum annealer was used to determine optimal machine layouts based on this new algorithm. The end result indicated that flow lines can be reduced by an average of 28% compared to existing machine layouts. OKI and OKI Data plan to refine these results to further increase productivity at the LED Management Factory.
"These results represent an advanced case of using a quantum annealer to optimize the layout of machines at an actual factory," said Kiyoshi Yokota, OKI's Chief Technology Officer and Head of Corporate Research & Development Center in the Corporate Infrastructure Group. "OKI is committed to working to achieve further practical applications of quantum computers in the future, thereby offering solutions to social issues, including increasing productivity to respond to workforce shortages."
As the working population in Japan shrinks, labor shortages are becoming an increasingly serious issue in manufacturing industries. Improving productivity at manufacturing sites has become a major and pressing social issue directly affecting manufacturing costs. At the LED Management Factory operated by OKI Data, multiple products are manufactured with different manufacturing processes using tens—or even hundreds—of different semiconductor manufacturing machines, with workers constantly moving between machines. Improving productivity here requires optimizing machine layouts to minimize distances traveled by workers ("flow lines"). However, as the numbers of machines and different types increase, the number of possible combinations increases exponentially. In the case examined here, this easily exceeds a googol (10 raised to the power of 100). Due to the need to account as well for complex constraints, including machine installation locations and methods of selecting duplicate machines, it was unfeasible to determine optimal machine layouts by calculating all of these parameters—even using a super computer or other high-performance conventional computer.
OKI and OKI Data used a quantum annealer provided by D-Wave to tackle this layout optimization. From a research perspective, a quantum annealer offers the advantage of facilitating quantitative observations of the results of the optimum layouts computed. However, to solve the problem in an efficient way, a new algorithm suited to constraints involving both the quantum annealer and the manufacturing site was required, making the involvement of personnel familiar with the manufacturing site absolutely essential. For this reason, personnel from the LED Management Factory were involved in the process to successfully design a computational algorithm in-house by modeling the conditions that apply when manufacturing two types of products involving different manufacturing processes and production quantities within the same factory. A quantum annealer was used to determine optimal machine layouts based on this new algorithm. The end result indicated that flow lines can be reduced by an average of 28% compared to existing machine layouts. OKI and OKI Data plan to refine these results to further increase productivity at the LED Management Factory.
"These results represent an advanced case of using a quantum annealer to optimize the layout of machines at an actual factory," said Kiyoshi Yokota, OKI's Chief Technology Officer and Head of Corporate Research & Development Center in the Corporate Infrastructure Group. "OKI is committed to working to achieve further practical applications of quantum computers in the future, thereby offering solutions to social issues, including increasing productivity to respond to workforce shortages."